What's Driving Manufacturing Growth?
Scott Stone January 14, 2015
ThomasNet’s latest Industry Market Barometer® survey of North American manufacturers highlights the growth of the industry: manufacturers are continuing to experience an upward trajectory, with more companies expanding, hiring, adding new product lines or services, and investing in future growth. Nearly eight out of ten (76%) manufacturers surveyed are now selling overseas, and the bulk of respondents are increasing production capacity, optimizing existing operations, and upgrading facilities in preparation for what’s to come.
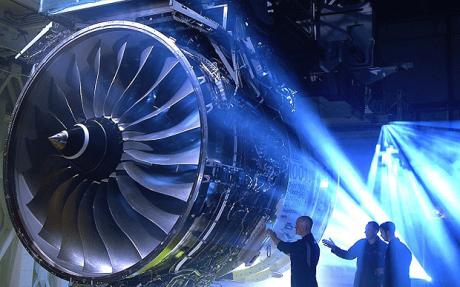
This rings true in Cisco-Eagle's experience. In general, the industrial economy seems to be in the best shape it has been since before the 2008 financial crisis, but manufacturing in particular is trending upward. We are seeing companies who have delayed capital projects begin to upgrade their operations, hire new workers, and generally catch up on optimizing their ability to serve their customers.
Here’s a closer look at Cisco-Eagle’s perspective on the IMB survey, as well as a few specific ways we are seeing our customers handle the flip side of continued manufacturing growth: the need to locate and hire the skilled workers necessary to sustain the trend.
Automation
More than a third (38%) of manufacturers who participated in this year’s IMB survey report they’ll leave their jobs in one to ten years, leaving the industry in “crisis mode” as companies look to fill these highly skilled positions.
From what we’ve observed, lack of skilled labor is an issue across all industrial operations, not just manufacturing. Distribution and warehousing operations are also looking for qualified workers. We have had many discussions with customers on automating certain areas of the warehouse, meaning they need to hire fewer total workers and focus on specific skillsets. Even in this scenario, however, companies struggle to find the right types of workers. We see companies openly recruiting machinists, welders, and skilled tradespeople of all types.
Some customers are also doing partial automation, which means automating one point in particular so that it requires fewer people. They are, for example, adding robots in specific applications, but may not be fully automating their facilities. Or they are adding solutions like carousels that help them recoup space and increase accuracy in tandem with either fully or partly automated workflows.
Lean Manufacturing & Sustainability
It’s not just about automation. Companies are going to 5S and lean operations that tend to create better workflows. Consolidating production lines and improving processes they are more logical and consistent reduces needless manual work, and allows companies to focus on the most important parts of their labor needs..
Our customer base is very concerned with sustainability and has been for some time. Even in the current situation, with falling oil prices (which is likely to be temporary), many still want and need to reduce energy consumption and become more sustainable. Automation is coming on strong, as the barriers to entry are lowering and the benefits are increasing. We are at the very front end of developments like advanced materials and 3D printing, which promise to help American manufacturing to recover more. Remember—the most compelling reason manufacturing was offshored was labor costs. When you reduce that as an advantage for overseas manufacturing, domestic operations are going to make their way back.
Younger Generation of Workers
One of the most shocking findings from the IMB report is that Millennials will comprise 75% of the workforce by the year 2025. That said, the question then becomes: How can we attract the type of talent the industry will need to fill the hundreds of thousands of positions left open when Baby Boomers retire?
We have been in an environment of manufacturing decline for so long that it’s easy to see why Millennials feel less than enthusiastic about their prospects in industry. If you grew up watching plant after plant close or cut back, would that be an easy sell as a career? Still, career opportunities exist for truly skilled craftspeople. Manufacturers who face skilled labor shortages must help restore their faith in these careers by rewarding those who put in the work to earn those skills – regardless of their age.
We have seen a shift in recent years when it comes to management of industrial operations. Companies are embracing new technology faster, which bodes well for younger workers who grew up in the interconnected internet/information economy. This hasn’t really filtered down as much to others who might take non-management manufacturing jobs. However, we predict it will eventually get there, as manufacturing companies add higher paying, skilled jobs. The seeds are in place to get this done, but it’s a definite cultural shift.
Final Thoughts
As manufacturing continues its upward trajectory, the question to ask is not what the sector can do to rebound from economic uncertainty but what it can do to maintain momentum. Based on our experience, three key ways manufacturers can sustain the existing growth are through automation, lean manufacturing principles, and investment in the younger generation of workers.
Did you find this useful?