Reduce Costs in Product Design Through Raw Materials
Martin Przeworski June 29, 2017
It is often later in the product lifecycle that procurement teams are brought in to lead a competitive bid process and conduct negotiations accordingly. This might seem like a straightforward approach to reducing costs. However, taking a deeper look at your product design and raw materials before the manufacturing phase could be the best way to proactively optimize costs.
This was the case for a building materials firm looking to produce a highly durable, but cost effective roof shingle composed of plastic. For manufactured plastic parts, the main components influencing finished unit price are the manufacturing process, the raw materials utilized within the formulation, and the design of the part. Often, the choice of materials is as crucial as the manufacturing process used. By taking a deeper look at your product’s design, and veering away from the standard materials and associated manufacturing processes, you might be surprised by the savings that can be achieved for the component parts.
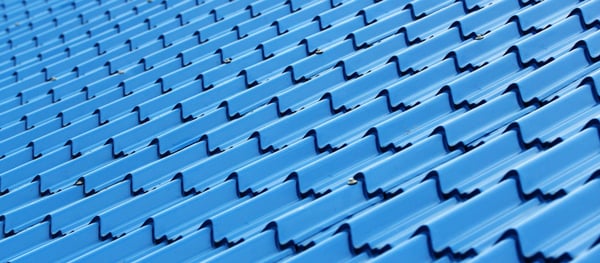
Let’s take a look at how this can be done:
Step 1: Defining the Functionality
Before deciding your raw materials or manufacturing processes, engineering teams need to fully define the functionality of the product.
- What is the primary function of the product?
- What quality is required of the product?
- What is the product’s size and complexity?
These and other factors will influence your material and manufacturing options. Fully defining the functionality of the product will serve as the foundation for decisions regarding your materials and manufacturing processes.
For the building materials manufacturer, cost was a top concern. In addition to cost, the shingle needed to be shatter resistant and survive various weather conditions.
Step 2: Assessing your materials and manufacturing options
With a clear idea of your product’s functionality, now is the time to assess the material and manufacturing options that fulfill the criteria.
Manufacturing Options
Since both injection molding and compression molding can be used to fabricate the same components we can concentrate on what the difference are between the two processes:
- Injection molding is perhaps the most common method of manufacturing smaller plastic parts that are used in everyday devices from cell phone bodies, phone cases, and car parts to bottle caps and those plastic forks we all use. The process consists of machining steel tooling or a mold in the negative shape of the part you want to make, then repeatedly feeding, melting, and injecting a chosen material such as a type of plastic into the mold to make thousands of copies of the part. The advantages of injection molding include the ability to create complex geometries, and repeatedly accurate parts in high volumes, while the disadvantages are centered around high tooling costs.
- Compression molding also utilizes a mold, but the material is loaded into the lower part of the mold, heated, then the top part of the mold is pressed into the bottom in order to form the finished part. In this way large flat or curved parts such as automotive body components can be manufactured. The biggest advantage of compression molding is the relatively low tooling and operational costs compared to other methods. The main disadvantages of compression molding include the inability to create very complex geometries, repeatability, flash trimming, and tool wear.
While these options are specific to plastic, general manufacturing process considerations are often centered on the complexity of the product., Depending on the product and volume, you might want to consider the most common manufacturing process to expand your options for cost saving purposes. You may also want to factor in the proximity of your manufacturer(s) to your materials supplier and/or your facility in terms of the logical costs to transport the materials and products.
Materials
Again, the materials you select will depend on your product’s functionality. This is a prime opportunity to assess your formulation options, bearing in mind that your materials and manufacturing processes are highly interrelated. During this step, you’ll want to form an understanding of what materials options will offer the same function, such as durability, flexibility, etc.
The building materials company we mentioned earlier usually chooses materials based on the plastic manufacturing process. Therefore, thermoset plastic parts are most often associated with compression molding, while both thermoplastic and thermoset materials are used with the injection molding process.
Thermoplastics such as ABS are the most common plastic materials in toys and electronics, while Acrylic is used as a replacement for glass in commercial offerings such as Plexiglass. This plastic material consists of polymers that are joined by intermolecular bonds, which are broken by heating and reformed by cooling, making the base material very recyclable and reusable.
On the other hand, thermosetting plastics or polymers start out as prepolymers that form chemical bonds with each other during the heating and curing process. Therefore, thermosets cannot be remelted and recycled like thermoplastics and are commonly recognizable as polyurethanes such as foams, shoe soles, mattresses, and adhesives.
From a practical point of view, one of the main manufacturing considerations is component size and tooling costs. Injection molding tends to be used for smaller components due to the high cost of tooling and the complexities of the injection process, while compression molding is used for larger parts and offers a low initial setup cost.
So, if you need your product to have higher mechanical strength, hardness, or just be more resistant to heat, the natural choice is to select a thermoset material and compression molding. This is the preferred formula for temperature resistant components and parts used in the electronics industry, which can often be glass filled.
For a low cost large commodity product, you might want to consider recyclable thermoplastic materials such as polyethylene (PE). They can be less expensive than thermoset materials and aren’t as brittle, making it the smarter choice if I you need high impact resistance as opposed to simple durability.
By combining the cost savings of recycled thermoplastic materials with other bulk filler materials and the advantage of compression molding to A non-conventional approach to plastic fabrication can offer. the best of both worlds. It enables you to combine the cost savings of recycled thermoplastic materials with other bulk filler materials and can accommodate larger footprint parts with the help of compression molding.
Step 3: Coming to a Decision in Design
Deciding the right design option for your product depends on your company’s unique product requirements. Through the process of exploring your options in the market, you should be in a much better position to design a product that matches your cost optimization and quality needs.
For the building materials company, optimizing their budget during the design phase was an ideal situation for their new product line. However, the same cost optimization process may also be generalized to other industries and products. This is a particularly ideal opportunity for Strategic Sourcing and Procurement teams (SS&P). By working with SS&P, engineers can get a broad view of the market and determine which manufacturing processes and raw materials suppliers are the most cost effective while maintaining fidelity of the component’s design and intended function.
Did you find this useful?