Optimize Safety In Industrial Operations To Drive Productivity & Revenue
Scott Stone January 14, 2020
Safety in the workplace is a serious matter — especially in industrial operations. In physically demanding and/or high-risk industries like many industrial operations, the implications of such injuries can be disastrous.
The latest U.S. Bureau of Labor Statistics data shows there were more than 5,200 fatal workplace injuries across all sectors, in addition to more than 3 million total recordable cases of non-fatal work-related injuries and illnesses in 2013.
Each year, manufacturers and distributors lose valuable manpower to slips, falls, and other accidents that hurt people, cause employees to miss work, and cost companies hundreds of thousands of dollars in workers’ compensation claims.
If you run a warehouse, manufacturing operation, or heavy commercial facility, practicing workplace safety isn’t just a good idea — it’s essential.
Although safety is a top priority in industrial operations, it's about more than just protecting workers. Promoting safety throughout the organization also helps to optimize worker productivity and drive revenue growth over both the near and the long term.
Let’s take a closer look at how.
Investing In All Your Employees
It’s no secret that the American industrial industry is undergoing a significant shift in workforce demographics as the older generation looks to retire in the coming years and younger workers increasingly enter the labor pool. In fact, Pew Research Center data shows that approximately 10,000 Baby Boomers will turn 65 every day for the next 19 years, which corresponds to increasing numbers of older workers retiring at an alarming rate.
But according to the U.S. Bureau Of Labor Statistics, workplace fatalities are trending upward among workers age 55 and older. In 2018, there were 1,863 fatal work injuries among workers age 55 and older. That was 35 percent of all workplace deaths, up from 20 percent in 1992.
For manufacturing and distribution companies, the time to start capturing the retiring workforce's safety knowledge is now. In other words, manufacturers and distribution centers need to set up a knowledge transfer process between new and retiring workers to promote safety best practices, as well as thwart any inefficiencies that might impede productivity. Implement a mentorship program for younger and older generations to share new ideas and tested tips. While some older workers may choose to work past retirement age, it's important that employees perform tasks that match their physical abilities. Encourage all your workers to take breaks as needed and work at their own pace. Consider assessing workplace noise hazards — some employees may not be as sensitive to higher noise levels as others.
While such an investment in workers and their safety requires due time, resources, and attention, a Penske blog on workplace safety notes that “every penny spent trying to prevent an accident is better than any expense dealing with the results of an accident.”
Ergonomics Contribute To Workplace Safety
Many of the workplace injuries highlighted by the Bureau of Labor Statistics could have been prevented in the first place with simple ergonomics.
Injuries aside, ergonomics also helps to promote worker productivity as well as improve morale. By reducing physical strain on the body (i.e., floor-level lifting, stretching to reach loads above or below arm level, or bending over for long periods of time), ergonomics allows workers to focus on the value-added work — not the amount of physical effort required to get the job done.
Check out these ergonomics consulting services listed on the Thomas Network.
As noted by Bishamon’s Bob Clark, “the right [ergonomic] equipment can not only alleviate heavy loads and increase the range of motion for workers, it can also lead to efficiencies that translate to profit for your bottom line.”
Do you provide ergonomic and safety consulting services for industrial operations too? List your business on the Thomas Network to grow your customer base.
Automation To Optimize Safety
While training is the foundation of all good safety programs — training and retraining not only remind employees how to be safe, but also reminds them why to be safe. With digital transformation of industrial companies on the rise, training programs can (and should) be augmented by safety automation.
In a recent Thomas Industrial Survey report, there has been a growing interest in automation adoption. More than half of the companies surveyed reported that they meet or exceed the industry standard for automation, with 55% of the participants being likely to very likely to invest in Production Performance Automation in the next 12 months.
When integrated into a well-planned safety training and safety process, automation can be a valuable asset because it reduces the need for workers to be in high-risk areas. As a result, workers can be redeployed to areas where they can be more productive and efficient. What’s more, companies can reinforce the importance of safety to employees across the organization.
“By using automated systems and intelligent software,” said SI Systems' Ed Romaine, “our organization can reduce walking, searching, and time spent delivering things. These are all different means of reducing the ergonomic strain on an individual, which helps enhance a company’s return on investment on their employees. It’s a win-win for everybody involved.”
Prioritizing Safety In Industrial Operations Is A Must
With the sheer volume of worker injuries, illnesses, and fatalities that occur each year in manufacturing and distribution operations, organizations must be prioritizing workplace safety at all times. Working to promote safer and more efficient industrial operations protects workers, and drives productivity and improves a company’s bottom line.
Related Articles For Industrial Growth:
- Technology That Can Improve Safety In Manufacturing and the Supply Chain
- How To Keep Up With Changing Technology Trends
- 11 Tips For Growing Your CNC Machining Business
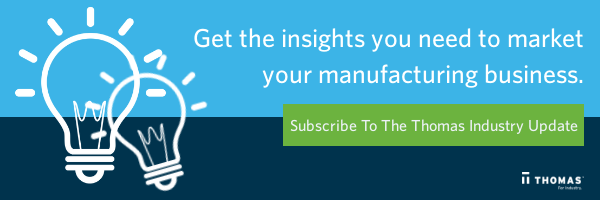
Did you find this useful?